ダウンホール化学物質注入ライン - なぜ失敗するのか?経験、挑戦、新しい試験法の応用
Copyright 2012、石油技術協会
概要
Statoil は、スケール防止剤のダウンホール連続注入が適用されるいくつかの油田を操業しています。目的は、上部チューブと安全弁を(Ba/Sr) SO4 または CaCO から保護することです。スケールの圧縮を定期的に実行するのが困難でコストがかかる場合、たとえば海底フィールドの結合など。
スケール防止剤のダウンホールへの連続注入は、生産パッカーの上にスケールが付着する可能性がある坑井の上部配管と安全弁を保護する技術的に適切な解決策です。特に、坑井付近の領域でスケールが発生する可能性があるため、定期的に絞る必要がない坑井では注意が必要です。
化学薬品注入ラインの設計、操作、保守では、材料の選択、化学物質の適格性評価、監視に特に重点を置く必要があります。圧力、温度、流量状況、システムの形状により、安全な操作に課題が生じる可能性があります。生産施設から海底鋳型までの数キロメートルにわたる注入ラインと、井戸内の注入バルブに課題が確認されています。
降水と腐食の問題に関するダウンホール連続注入システムの複雑さを示す現場の経験について説明します。実験室での研究と化学適格性評価のための新しい方法の応用を代表しています。学際的な活動のニーズに対応します。
序章
Statoil は、化学薬品のダウンホール連続注入が適用されているいくつかの油田を運営しています。これには主にスケール防止剤 (SI) の注入が含まれ、その目的は上部管とダウンホール安全弁 (DHSV) を (Ba/Sr) SO4 または CaCO から保護することです。規模。場合によっては、エマルジョンブレーカーを坑井内に注入して、比較的高温で坑井のできるだけ深いところで分離プロセスを開始します。
スケール防止剤のダウンホールへの連続注入は、生産パッカーの上でスケールの可能性がある坑井の上部を保護する技術的に適切な解決策です。連続注入は、特に、坑井付近でのスケーリングの可能性が低いため、絞る必要のない坑井では推奨される場合があります。または、スケールの圧縮を定期的に実行するのが困難でコストがかかる場合(たとえば、海底フィールドの結合など)。
Statoil は、表層システムおよび海底テンプレートへの連続化学薬品注入の経験を積んできましたが、新たな課題は、注入ポイントを坑井のさらに深くすることです。化学薬品注入ラインの設計、操作、保守には、いくつかのトピックに特に重点を置く必要があります。材料の選択、化学物質の認定、モニタリングなど。圧力、温度、流量状況、システムの形状により、安全な操作に課題が生じる可能性があります。生産施設から海底テンプレート、そして井戸内の注入バルブまでの長い(数キロメートル)注入ラインにおける課題が特定されています。図1。噴射システムの中には計画通りに機能したものもあれば、さまざまな理由で失敗したものもあります。ダウンホール化学注入 (DHCI) のために、いくつかの新しいフィールド開発が計画されています。しかし;場合によっては、機器がまだ完全に認定されていない場合があります。
DHCI の適用は複雑な作業です。これには、完成と坑井の設計、坑井の化学反応、トップサイドシステム、トップサイドプロセスの化学物質投与システムが含まれます。化学物質は、化学物質注入ラインを介して上面から完成装置までポンプで汲み上げられ、坑井に下降します。したがって、この種のプロジェクトの計画と実行では、複数の分野間の協力が重要です。さまざまな考慮事項を評価する必要があり、設計中の良好なコミュニケーションが重要です。プロセスエンジニア、海底エンジニア、完成エンジニアが関与し、坑井化学、材料選択、流量保証、生産化学物質管理などのテーマに取り組んでいます。課題としては、化学ガンキングや温度安定性、腐食、さらに場合によっては化学薬品注入ライン内の局所的な圧力や流量の影響による真空効果などが挙げられます。これらに加えて、高圧、高温、高いガス流量、高いスケール付着の可能性などの条件,長距離の臍帯と井戸内の深い注入ポイントにより、注入される化学薬品と注入バルブにさまざまな技術的課題と要件が与えられます。
Statoil の運用に設置された DHCI システムの概要は、その経験が常に成功しているわけではないことを示しています (表 1)。ただし、注入設計、化学物質の認定、運用および保守の改善計画が行われています。課題は分野ごとに異なり、必ずしも薬液注入バルブ自体が機能していないことが問題であるとは限りません。
ここ数年にわたり、ダウンホール化学物質注入ラインに関するいくつかの課題が経験されてきました。この文書では、これらの経験からいくつかの例を示します。この文書では、DHCI 回線に関連する課題とその解決策について説明します。2 つの症例履歴が示されています。1 つは腐食に関するもの、もう 1 つは化学銃の王に関するものです。降水と腐食の問題に関するダウンホール連続注入システムの複雑さを示す現場の経験について説明します。
実験室での研究や化学的認定のための新しい方法の適用も考慮されます。化学薬品をポンプで送り込む方法、スケールの可能性と防止、複雑な装置の用途、化学薬品が再生成されたときに化学薬品が上面システムにどのような影響を与えるか。化学用途の受け入れ基準には、環境問題、効率、上部の貯蔵容量、ポンプ速度、既存のポンプが使用できるかどうかなどが含まれます。技術的な推奨事項は、流体と化学の適合性、残留検出、材料の適合性、海中臍帯設計、化学薬品投与システムに基づいている必要があります。およびその周囲のマテリアル。ガスの侵入による注入ラインの詰まりを防ぐために、化学物質は水和物を抑制する必要がある場合があり、化学物質は輸送および保管中に凍結しないようにする必要があります。既存の内部ガイドラインには、システムの各ポイントでどの化学物質を適用できるかのチェックリストがあります。粘度などの物理的特性が重要です。注入システムは、臍帯海底流線の距離が 3 ~ 50 km、井戸までの距離が 1 ~ 3 km であることを意味している可能性があります。したがって、温度安定性も重要です。例えば製油所における下流への影響の評価も考慮する必要があるかもしれません。
ダウンホール化学薬品注入システム
コストメリット
DHS または生産チューブを保護するためにスケール防止剤をダウンホールに継続的に注入することは、スケール防止剤で坑井を絞るよりも費用効果が高い可能性があります。このアプリケーションは、スケール圧搾処理と比較して地層損傷の可能性を低減し、スケール圧搾後のプロセス問題の可能性を低減し、トップサイド注入システムからの化学薬品注入速度を制御する可能性を与えます。この注入システムは、他の化学薬品をダウンホールに連続的に注入するために使用することもでき、それによってプロセスプラントのさらに下流で発生する可能性のある他の課題を軽減できます。
オーセバーグ S またはフィールドのダウンホールスケール戦略を開発するための包括的な研究が実施されました。大規模な懸念は CaCO でした。上部チューブにスケールが発生し、DHSV が故障する可能性があります。オーセバーグ S またはスケール管理戦略の検討では、3 年間にわたって、化学物質注入ラインが機能していた坑井では DHCI が最もコスト効率の高いソリューションであると結論付けられました。競合するスケールスクイーズ技術に関する主なコスト要素は、化学薬品や運用コストではなく、繰延石油でした。ガスリフトにスケール防止剤を使用する場合、ケミカルガンキングを避けるために濃度とガスリフト速度のバランスをとる必要があるため、化学薬品コストの主な要因は高いガスリフト速度であり、高い SI 濃度につながりました。オーセバーグ S の 2 つのウェル、または良好に機能する DHC I ラインを備えた 2 つのウェルでは、DHS V を CaCO から保護するためにこのオプションが選択されました。スケーリング。
連続噴射システムとバルブ
連続化学薬品注入システムを使用した既存の完成ソリューションは、キャピラリ ラインの詰まりを防ぐという課題に直面しています。通常、注入システムは、外径 (OD) 1/4 インチまたは 3/8 インチのキャピラリ ラインで構成され、表面マニホールドに接続され、チューブの環状側にあるチューブ ハンガーに供給されて接続されます。キャピラリ ラインは、特殊なチューブ カラー クランプによって製造チューブの外径に取り付けられ、チューブの外側を化学薬品注入マンドレルまで伸びています。マンドレルは伝統的に、注入された化学物質に十分な分散時間を与え、問題が見つかった場所に化学物質を配置することを目的として、DHS V の上流または坑井のより深くに配置されます。
化学薬品注入バルブ (図 2) には、直径約 1.5 インチの小さなカートリッジに、坑井の流体が毛細管ラインに入るのを防ぐ逆止弁が含まれています。それは、バネの上に乗っている単なる小さなポペットです。ばね力は、ポペットをシールシートから外すために必要な圧力を設定および予測します。薬液が流れ始めると、ポペットがシートから持ち上げられ、逆止弁が開きます。
逆止弁を2個取り付ける必要があります。1 つのバルブは、坑井の流体が毛細管ラインに入るのを防ぐ主な障壁です。これは比較的低い開口圧力 (2 ~ 15 バール) を持っています。毛細管ライン内の静水圧が坑井内圧力よりも低い場合、坑井内流体は毛細管ラインに入ろうとします。もう 1 つの逆止弁は、130 ~ 250 バールの異常な開放圧力を持ち、U チューブ防止システムとして知られています。このバルブは、キャピラリーライン内の静水圧が生産チューブ内の化学物質注入点における坑井の圧力よりも高い場合に、キャピラリーライン内の化学物質が坑井内に自由に流れるのを防ぎます。
2 つの逆止弁に加えて、通常はインライン フィルターがあります。この目的は、いかなる種類の破片も逆止弁システムのシール機能を損なうことがないようにすることです。
説明されている逆止弁のサイズはかなり小さく、注入される流体の清浄度はその動作機能にとって不可欠です。システム内の破片は、毛細管ライン内の流量を増加させて逆止弁を意図的に開くことによって洗い流すことができると考えられています。
逆止弁が開くと、流れる圧力は急速に減少し、圧力が再び増加するまで毛細管ラインを上に伝播します。逆止弁は、化学薬品の流れがバルブを開くのに十分な圧力を蓄積するまで閉じます。その結果、逆止弁システム内で圧力振動が発生します。逆止弁システムの開放圧力が高くなるほど、逆止弁が開いてシステムが平衡状態に到達しようとするときに確立される流路面積が小さくなります。
薬液注入バルブの開放圧力は比較的低いです。また、化学薬品入口点のチューブ圧力が、キャピラリー ライン内の化学薬品の静水圧と逆止弁の開口圧力の合計よりも低くなると、キャピラリー ラインの上部では真空または真空に近い状態が発生します。化学物質の注入が停止するか、化学物質の流量が少なくなると、キャピラリ ラインの上部でほぼ真空状態が発生し始めます。
真空レベルは、坑井の圧力、キャピラリーライン内で使用される注入された化学混合物の比重、注入点での逆止弁の開放圧力、およびキャピラリーライン内の化学物質の流量によって決まります。油井の状態はフィールドの寿命にわたって変化するため、真空の可能性も時間の経過とともに変化します。予想される問題が発生する前に、この状況を認識し、適切な考慮と予防措置を講じることが重要です。
通常、この種の用途で使用される溶媒は、注入率が低いことに加えて蒸発し、十分に調査されていない影響を引き起こします。これらの影響は、溶媒が蒸発する際のガンキングまたは固体 (ポリマーなど) の沈殿です。
さらに、ガルバニ電池は、化学薬品の流体表面とその上の蒸気で満たされたほぼ真空の気相との間の遷移相で形成され得る。このような条件下では化学物質の攻撃性が高まるため、キャピラリ ライン内部に局所的な孔食が発生する可能性があります。キャピラリーラインの内部が乾燥するにつれて、キャピラリーライン内の膜として形成されたフレークまたは塩の結晶は、キャピラリーラインを詰まらせたり詰まらせたりする可能性があります。
井戸バリアの哲学
堅牢な坑井ソリューションを設計する場合、Statoil は坑井のライフサイクル全体にわたって坑井の安全性が常に確保されていることを要求します。したがって、Statoil では、2 つの独立した坑井バリアが無傷であることが必要です。図 3 は、典型的なウェルバリアの概略図を示しており、青色は主要なウェルバリアエンベロープを表しています。この場合は製造チューブです。赤色は二次バリアエンベロープを表します。ケーシング。スケッチの左側では、化学物質の注入が黒い線で示されており、赤でマークされた領域 (二次バリア) の製造チューブへの注入点が示されています。化学物質注入システムを坑井に導入すると、一次坑井と二次坑井の両方の障壁が危険にさらされます。
腐食の事例履歴
イベントの順序
スケール抑制剤のダウンホール化学注入が、ノルウェー大陸棚にあるスタトイルによって運営されている油田に適用されました。この場合、適用されたスケール防止剤は、もともと表層および海底への適用に適格なものでした。井戸の再完成に続いて、DHCIpointat2446mMD が設置されました (図 3)。トップサイドスケール防止剤のダウンホール注入は、化学物質のさらなる試験を行わずに開始されました。
1 年間の稼働後、化学薬品注入システムの漏れが観察され、調査が開始されました。漏れは井戸の障壁に悪影響を及ぼしました。同様の出来事がいくつかの井戸で発生し、調査の進行中、一部の井戸は閉鎖されなければなりませんでした。
生産チューブを引き抜き、詳細に研究しました。腐食はチューブの片側に限定されており、一部のチューブ接合部は実際に穴が開くほど腐食していました。厚さ約 8.5 mm の 3% クロム鋼は 8 か月以内に崩壊しました。主な腐食は坑口から約 380m MD までの坑井の上部で発生しており、最もひどい腐食が見られた配管接合部は約 350m MD 付近で見つかりました。この深さより下では腐食はほとんど、またはまったく観察されませんでしたが、チューブの外径に多くの破片が見つかりました。
9-5/8 インチのケーシングも切断して引っ張ると、同様の効果が観察されました。ウェルの上部セクションの片側のみに腐食が見られます。誘発された漏れは、ケーシングの脆弱な部分が破裂することによって引き起こされました。
薬液注入ラインの材質は合金 825 でした。
化学的資格
化学的特性と腐食試験は、スケール防止剤の認定において重要な焦点であり、実際のスケール防止剤は認定され、数年間にわたって表層および海中の用途で使用されてきました。実際のダウンホール薬剤を適用した理由は、既存のダウンホール薬剤を置き換えることにより環境特性を向上させるためであった。しかし、スケール防止剤は、周囲の表層および海底温度(4〜20℃)でのみ使用されていた。井戸に注入されるとき、化学物質の温度は 90℃ に達する可能性がありますが、この温度でのさらなる試験は行われていませんでした。
化学品供給業者によって初期の腐食性テストが実施され、その結果は高温での炭素鋼の腐食性が 2 ~ 4 mm/年であることを示しました。この段階では、オペレーターの重大な技術的能力の関与は最小限でした。その後、オペレーターによって新たなテストが実施され、スケール防止剤が製造チューブおよび製造ケーシングの材料に対して非常に腐食性が高く、腐食速度が 70 mm/年を超えていることが判明しました。化学薬品注入ラインの材料である合金 825 は、注入前にスケール防止剤に対してテストされていませんでした。坑井の温度は 90℃ に達する可能性があり、これらの条件下で適切なテストを実行する必要があります。
調査では、濃縮溶液としてのスケール防止剤の pH が 3.0 未満であることも明らかになりました。ただし、pHは測定されていませんでした。その後、測定された pH は、pH 0 ~ 1 の非常に低い値を示しました。これは、所定の pH 値に加えて、測定と材料の考慮が必要であることを示しています。
結果の解釈
注入ライン (図 3) は、注入点で坑井内の圧力を超えるスケール防止剤の静水圧を与えるように構成されています。抑制剤は坑井内に存在する圧力よりも高い圧力で注入されます。これにより、ウェルの閉鎖時に U チューブ効果が発生します。バルブは常に、坑井内よりも注入ライン内の圧力が高いときに開きます。したがって、注入ライン内で真空または蒸発が発生する可能性があります。腐食速度と孔食の危険性は、溶媒の蒸発により気体/液体遷移ゾーンで最も大きくなります。クーポンに対して行われた実験室実験により、この理論が確認されました。漏洩が発生した井戸では、注入ラインの穴はすべて薬液注入ラインの上部に位置していました。
図 4 は、顕著な孔食のある DHC I ラインの写真を示しています。外側の製造チューブに見られた腐食は、孔食漏れ点からのスケール防止剤の局所的な露出を示していました。漏洩の原因は、腐食性の高い薬液による孔食と、薬液注入ラインから生産ケーシングへの漏洩でした。スケール防止剤が穴の開いたキャピラリ ラインからケーシングとチューブに噴霧され、漏れが発生しました。注入ラインの漏れによる二次的な影響は考慮されていませんでした。ケーシングとチューブの腐食は、穴のある毛細管ラインからケーシングとチューブに付着した濃縮されたスケール抑制剤の結果であると結論付けられました (図 5)。
このケースでは、材料専門の技術者の関与が不足していました。DHCI ライン上の化学物質の腐食性はテストされておらず、漏れによる二次的な影響も評価されていませんでした。周囲の材料が化学物質への曝露に耐えられるかどうかなど。
化学銃王の事件史
イベントの順序
HP HT フィールドのスケール防止戦略は、ダウンホール安全弁の上流にスケール防止剤を継続的に注入することでした。重度の炭酸カルシウムスケールの可能性が井戸内で確認されました。課題の 1 つは、高温、高いガスと凝縮水の生成速度と、低い水生成速度の組み合わせでした。スケール防止剤を注入することによる懸念は、高いガス生成速度によって溶媒が除去され、井戸内の安全弁の上流の注入点で化学物質のガンキングが発生することでした (図 1)。
スケール防止剤の認定では、トップサイド プロセス システム (低温) での挙動を含む、HP HT 条件での製品の効率に焦点が当てられました。高いガス速度による生産チューブ内でのスケール防止剤自体の沈殿が主な懸念事項でした。臨床検査では、スケール防止剤が沈殿してチューブの壁に付着する可能性があることが示されました。したがって、安全弁の作動によりリスクを回避できる可能性があります。
経験上、数週間の稼働後に化学薬品ラインが漏れていることが分かりました。キャピラリラインに設置された表面ゲージで坑井の圧力を監視することができました。ウェルの完全性を得るためにラインを分離しました。
化学物質注入ラインが井戸から引き抜かれ、開いて検査され、問題を診断し、考えられる故障の原因が特定されました。図6に見られるように、かなりの量の沈殿物が見つかり、化学分析により、この一部がスケール防止剤であることが示されました。沈殿物はシールとポペットに位置しており、バルブは操作できませんでした。
バルブの故障は、バルブシステム内の破片が逆止弁の金属対金属シートの食い込みを妨げていたことが原因でした。破片を検査したところ、主な粒子は金属の削りくずであり、おそらくキャピラリラインの設置プロセス中に生成されたものであることが判明した。さらに、両方の逆止弁、特に弁の裏側にいくつかの白い破片が確認されました。これは低圧側です。つまり、この側は常に坑井の流体と接触します。当初、バルブが開いたままになっていて坑井の流体にさらされていたため、これは生産坑井からの破片であると考えられていました。しかし、その破片を検査したところ、スケール防止剤として使用された化学物質と同様の化学的性質を持つポリマーであることが判明した。これは私たちの興味を引き、Statoil は毛細管ラインに存在するこれらのポリマー破片の背後にある理由を調査したいと考えました。
化学的資格
HP HT 分野では、製造上のさまざまな問題を軽減するための適切な化学物質の選択に関して多くの課題があります。ダウンホール連続注入用スケール防止剤の認定では、次のテストが実行されました。
●製品の安定性
●熱老化
● 動的性能テスト
● 地層水および水和物抑制剤(MEG)との適合性
● 静的および動的ガンキングテスト
●再溶解情報水、 フレッシュケミカルとMEG
化学薬品はあらかじめ決められた投与量で注入されます,しかし、水の生産量は必ずしも一定ではありません,つまり水スラッギング。ミズナメクジの間,化学物質が坑井に入ったとき,それは熱いもので迎えられるだろう,炭化水素ガスの速い流れ。これは、ガス リフト用途でスケール防止剤を注入するのと似ています (Fleming et al.2003)。
高いガス温度,溶剤が剥離する危険性が非常に高く、ガンキングにより注入バルブが詰まる可能性があります。これは、高沸点/低蒸気圧の溶媒やその他の蒸気圧降下剤 (VPD) を使用して配合された化学物質であってもリスクです。,地層水の流れ,MEG および/または新しい化学物質は、脱水または汚れた化学物質を除去または再溶解できなければなりません。
この場合、生産システムとしての HP/HTg の注入ポート付近の流動条件を再現するために、新しい実験室テスト装置が設計されました。ダイナミックガンキングテストの結果は、提案された塗布条件下で大幅な溶剤損失が記録されたことを示しています。これにより、急速なガンキングが発生し、最終的には動線が遮断される可能性があります。したがって、この研究では、水の生産前にこれらの井戸に継続的に化学薬品を注入することには比較的重大なリスクが存在することが実証され、この油田の通常の起動手順を調整し、水の突破が検出されるまで化学薬品の注入を遅らせる決定につながりました。
連続注入ダウンホール用のスケール防止剤の適格性評価では、注入点およびフローラインにおけるスケール防止剤の溶剤ストリッピングとガンキングに重点が置かれていましたが、注入バルブ自体のガンキングの可能性は評価されていませんでした。おそらく溶媒の大幅な損失と急速なガンキングにより、注入バルブが故障したと考えられます,図6. 結果は、システムの全体像を把握することが重要であることを示しています;生産上の課題だけに焦点を当てるだけではなく、,だけでなく、化学薬品の注入に関連する課題もある,つまりインジェクションバルブです。
他分野での経験
長距離の化学物質注入ラインの問題に関する初期の報告の 1 つは、ガル ファク サンドヴィグ ディス衛星フィールドからのものでした (Osa et al.2001)。海中注入ラインは、生成された流体からのガスの侵入により、ライン内でのハイドレート形成が妨げられました。インジェクションバルブを介してラインに注入されます。海中生産化学物質の開発のための新しいガイドラインが開発されました。要件には、粒子の除去 (濾過) と、海底テンプレートに注入されるすべての水ベースのスケール防止剤への水和物防止剤 (グリコールなど) の追加が含まれます。化学的安定性,粘度や相溶性(液体と材料)も考慮しました。これらの要件は Statoil システムにもさらに取り入れられており、ダウンホールの化学物質注入も含まれています。
Oseberg S または油井の開発段階では、すべての井戸を DHC I システムで完成させることが決定されました (Fleming et al.2006)。目的は、CaCO を防ぐことでした。;SI注入による上部チューブのスケーリング。化学薬品注入ラインに関する主要な課題の 1 つは、地表とダウンホール出口の間の通信を実現することでした。化学薬品注入ラインの内径は、スペースの制限によりアニュラス安全弁の周囲で 7 mm から 0.7 mm (ID) に狭くなり、このセクションを通って輸送される液体の能力が成功率に影響していました。いくつかのプラットフォーム井戸では化学薬品注入ラインが詰まっていました,しかしその理由は分かりませんでした。さまざまな流体(グリコール)の列,粗雑な,凝縮水,キシレン,スケール防止剤,水など)は実験室で粘度と適合性がテストされ、順方向および逆方向にポンプで送られてラインが開きます。;しかし,ターゲットのスケール抑制剤を薬液注入バルブまでポンプで送り込むことができませんでした。さらに遠く,合併症は、1 つの井戸内で残留 CaCl z 完了ブラインとともにホスホン酸塩スケール抑制剤が沈殿し、軽油比が高く水カットが低い井戸内でスケール抑制剤が大量に沈殿することが見られました (Fleming et al.2006)。
学んだ教訓
試験法の開発
DHC I システムの失敗から学んだ主な教訓は、スケール防止剤の技術的効率に関するものであり、機能性や化学物質の注入に関するものではありません。上面噴射と海底噴射は長期にわたり良好に機能している;しかし,この適用は、化学的認定方法の対応する更新を行わずに、ダウンホール化学物質注入に拡張されました。提示された 2 つの現場事例から得た Statoil の経験では、化学的認定に関する管理文書またはガイドラインは、このタイプの化学的用途を含めるように更新する必要があるということです。主な 2 つの課題は、i) 化学薬品注入ライン内の真空、および ii) 化学薬品の潜在的な沈殿であると特定されています。
化学物質の蒸発は製造チューブ (ガンキングのケースで見られるように) で発生する可能性があり、注入チューブ (真空のケースでは一時的な界面が確認されています) でこれらの沈殿物が流れとともに移動し、インジェクションバルブへ、さらにウェルへ。噴射バルブは、多くの場合、噴射ポイントの上流にフィルターを備えた設計になっています。,これは挑戦です,降水の場合と同様に、このフィルターが詰まってバルブが故障する可能性があります。
学んだ教訓からの観察と暫定的な結論により、現象に関する大規模な実験室研究が行われました。全体的な目的は、将来同様の問題を回避するための新しい認定方法を開発することでした。この研究では、特定された課題に関して化学物質を検査するために、さまざまな試験が実施され、いくつかの実験室手法が設計(目的として開発)されました。
● 密閉システムにおけるフィルターの詰まりと製品の安定性。
● 溶剤の部分的損失が化学薬品の腐食性に及ぼす影響。
● キャピラリー内での部分的な溶媒損失が固体または粘性プラグの形成に及ぼす影響。
実験室での方法のテスト中に、いくつかの潜在的な問題が特定されました
●フィルターの目詰まりを繰り返し、安定性が低下します。
● キャピラリーからの部分蒸発後の固体形成
●溶媒の損失によりPHが変化します。
実施されたテストの性質により、特定の条件にさらされたときの毛細管内の化学物質の物理的特性の変化に関する追加の情報と知識も提供されています。,そして、これが同様の条件にさらされたバルク溶液とどのように異なるのか。テスト作業では、バルク流体間の大きな違いも特定しました。,蒸気相および残留流体は、沈殿の可能性の増加および/または腐食性の増加につながる可能性があります。
スケール防止剤の腐食性の試験手順が開発され、管理文書に組み込まれました。スケール防止剤の注入を実施する前に、用途ごとに拡張腐食性試験を実行する必要がありました。注入ライン内の化学薬品のガンキングテストも実施されました。
化学物質の認定を開始する前に、化学物質の課題と目的を説明する作業範囲を作成することが重要です。初期段階では、問題を解決する化学物質の種類を選択できるように、主な課題を特定することが重要です。最も重要な合格基準の概要を表 2 に示します。
化学品の認定
化学物質の認定は、各用途の試験と理論的評価の両方で構成されます。技術仕様とテスト基準を定義および確立する必要がある,たとえばHSE内で,材料の適合性,製品の安定性と製品の品質(粒子)。さらに遠く,氷点,粘度および他の化学物質との適合性,水和物阻害剤,地層水と生成された流体を決定する必要があります。化学物質の認定に使用される可能性のある試験方法の簡略化されたリストを表 2 に示します。
技術効率への継続的な焦点と監視,線量率と HSE の事実は重要です。製品の要件によって、現場やプロセスプラントの寿命が変わる可能性があります;生産速度や流体の組成によって異なります。業績評価によるフォローアップ活動,最適な治療プログラムを確保するには、新しい化学物質の最適化やテストを頻繁に行う必要があります。
オイルの質にもよりますが,海洋生産プラントにおける水の生産と技術的課題,輸出品質を達成するには、生産用化学薬品の使用が必要になる場合があります,規制要件,そして海洋施設を安全な方法で運用すること。すべての分野には異なる課題があり、必要な生産用化学物質は分野ごと、時間の経過とともに異なります。
認定プログラムでは、生産化学物質の技術的効率に焦点を当てることが重要です,しかし、化学物質の特性に焦点を当てることも非常に重要です。,安定性などの,製品の品質と互換性。この設定での適合性は、流体との適合性を意味します。,材料およびその他の製造用化学物質。これは難しいことかもしれません。問題を解決するために化学物質を使用し、後でその化学物質が新たな課題の一因となったり新たな課題を生み出したりすることが判明することは望ましくありません。おそらく最大の課題は技術的な課題ではなく、化学物質の特性です。
特別な要件
供給される製品の濾過に関する特別な要件は、海底システムおよび連続注入ダウンホールに適用される必要があります。薬液注入システムのストレーナおよびフィルタは、トップサイド注入システムから下流の機器の仕様に基づいて提供する必要があります。,ポンプとインジェクションバルブ,ダウンホール噴射弁へ。化学物質のダウンホール連続注入が適用される場合、化学物質注入システムの仕様は最も重要度の高い仕様に基づく必要があります。おそらくインジェクションバルブのダウンホールにあるフィルターでしょう。
インジェクションの課題
注入システムは、臍帯海底流路の距離が 3 ~ 50 km、井戸までの距離が 1 ~ 3 km であることを意味している可能性があります。粘度や化学物質をポンプで送り出す能力などの物理的特性が重要です。海底温度での粘度が高すぎる場合、海底臍帯の化学物質注入ラインを通って海底注入点または井戸に化学物質を注入することが困難になる可能性があります。粘度は、予想される保管温度または使用温度でのシステム仕様に従っている必要があります。これはケースごとに評価する必要があります,システムに依存します。表のように、薬液注入率は薬液注入の成功の要因です。化学薬品注入ラインが詰まるリスクを最小限に抑えるため,このシステム内の化学物質は、水和物を抑制する必要があります (水和物の可能性がある場合)。システム内に存在する液体 (保存液) および水和物防止剤との適合性を確認する必要があります。実際の温度(可能な限り低い周囲温度)での化学物質の安定性試験,周囲温度,海底温度,射出温度)を通過する必要があります。
一定の頻度で薬液注入ラインを洗浄するプログラムも考慮する必要があります。定期的に薬液注入ラインを溶剤で洗い流すことで予防効果が得られる場合があります,グリコールまたは洗浄剤を使用して、堆積物が蓄積してラインの詰まりを引き起こす前に除去します。フラッシング液の薬液は以下のものを選択してください。注入ラインの化学薬品との互換性があります。
場合によっては、化学薬品注入ラインは、現場の寿命や流体条件にわたるさまざまな課題に基づいて、いくつかの化学用途に使用されます。水の突破前の初期生産段階では、主な課題は、多くの場合水生産量の増加に関連する寿命後半の課題とは異なる場合があります。アスファルテン防止剤などの非水溶媒ベースの防止剤からスケール防止剤などの水ベースの化学薬品に変更すると、適合性に問題が生じる可能性があります。したがって、化学薬品注入ラインで化学薬品を変更することが計画されている場合は、スペーサーの適合性、認定および使用法に焦点を当てることが重要です。
材料
材質の適合性について,すべての化学薬品はシールと互換性がある必要があります,エラストマー,化学薬品注入システムおよび生産プラントで使用されるガスケットおよび建設資材。ダウンホール連続注入用の化学物質(酸性スケール防止剤など)の腐食性の試験手順を開発する必要があります。化学物質の注入を実施する前に、用途ごとに拡張腐食性試験を行う必要があります。
議論
連続ダウンホール化学薬品注入の長所と短所を評価する必要があります。DHS または生産チューブを保護するためにスケール抑制剤を継続的に注入することは、油井をスケールから保護するための優れた方法です。この論文で述べたように、連続ダウンホール化学薬品注入にはいくつかの課題があります。,ただし、リスクを軽減するには、解決策に関連する現象を理解することが重要です。
リスクを軽減する 1 つの方法は、テスト方法の開発に重点を置くことです。上部または海底の化学薬品注入と比較すると、坑井内では異なるより厳しい条件が存在します。ダウンホールへの化学物質の連続注入のための化学物質の認定手順では、これらの条件の変化を考慮する必要があります。化学物質の認定は、化学物質が接触する可能性のある物質に応じて行われなければなりません。これらのシステムが動作するさまざまな油井のライフサイクル条件にできるだけ近い条件での互換性認定とテストの要件を更新し、実装する必要があります。テスト方法の開発は、より現実的で代表的なテストにさらに発展する必要があります。
加えて,化学物質と装置の間の相互作用は成功のために不可欠です。化学薬品注入バルブの開発では、化学的特性と坑井内の注入バルブの位置を考慮する必要があります。試験装置の一部として実際の噴射バルブを組み込み、認定プログラムの一部としてスケール抑制剤とバルブ設計の性能試験を実施することを考慮する必要があります。スケール防止剤を認定するには,以前はプロセスの課題とスケール抑制に主な焦点が当てられてきました。,しかし、良好なスケール抑制は、安定した継続的な注入に依存します。安定した継続的な注入がなければ、スケールが発生する可能性が高くなります。スケール防止剤注入バルブが汚れていて、流体の流れにスケール防止剤が注入されていない場合,油井と安全弁はスケールから保護されていないため、安全な生産が危険にさらされる可能性があります。認定手順では、プロセスの課題と認定されたスケール抑制剤の効率に加えて、スケール抑制剤の注入に関連する課題にも対処する必要があります。
新しいアプローチにはいくつかの分野が関係しており、分野間の協力とそれぞれの責任を明確にする必要があります。このアプリケーションでは、トップサイドプロセスシステム,海底テンプレートと坑井の設計と完成が含まれます。化学薬品注入システム用の堅牢なソリューションの開発に焦点を当てた複数の専門分野のネットワークが重要であり、おそらく成功への近道です。さまざまな分野間のコミュニケーションが重要です;特に、適用される化学薬品を管理する化学者と坑井で使用される機器を管理する坑井技術者との間の緊密なコミュニケーションが重要です。プロセス全体の複雑さを理解するには、さまざまな分野の課題を理解し、互いに学び合うことが不可欠です。
結論
● スケール防止剤を継続的に注入して DHS V を保護するか、生産チューブは油井をスケールから保護する優れた方法です
● 特定された課題を解決するため,次の推奨事項は:
● 専用の DHCI 認定手順を実行する必要があります。
●薬液注入バルブの認定方法
● 化学的機能性の試験および認定方法
● 手法の開発
● 関連する材料試験
● 関係するさまざまな分野間のコミュニケーションが成功には不可欠である、多分野の交流。
謝辞
著者は、この研究の出版を許可してくれた Statoil AS A と、図 2 の画像の使用を許可してくれた Baker Hughes と Schlumberger に感謝したいと思います。
命名法
(Ba/Sr)SO4=硫酸バリウム/硫酸ストロンチウム
CaCO3=炭酸カルシウム
DHCI=ダウンホール化学物質注入
DHSV=ダウンホール安全弁
例=たとえば
GOR=軽油比率
HSE=健康安全環境
HPHT=高圧高温
ID=内径
つまり=つまり
km=キロメートル
mm=ミリメートル
MEG=モノエチレングリコール
mMD=メートル測定深度
OD=外径
SI=スケール防止剤
mTV D=垂直方向の合計深さメートル
Uチューブ=U字管
VPD=蒸気圧降下剤
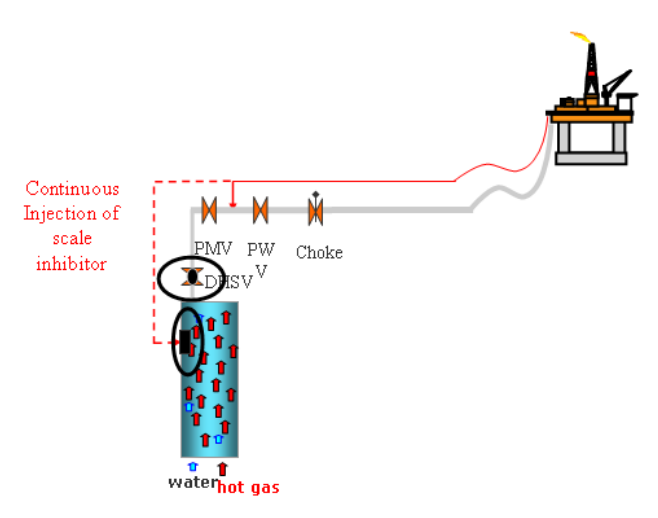
図 1. 非典型的なフィールドにおける海中およびダウンホール化学注入システムの概要。DHSV 上流の化学物質注入の概略図と、それに関連して予想される課題。DHS V= ダウンホール安全バルブ、PWV= プロセス ウィング バルブ、PM V= プロセス マスター バルブ。
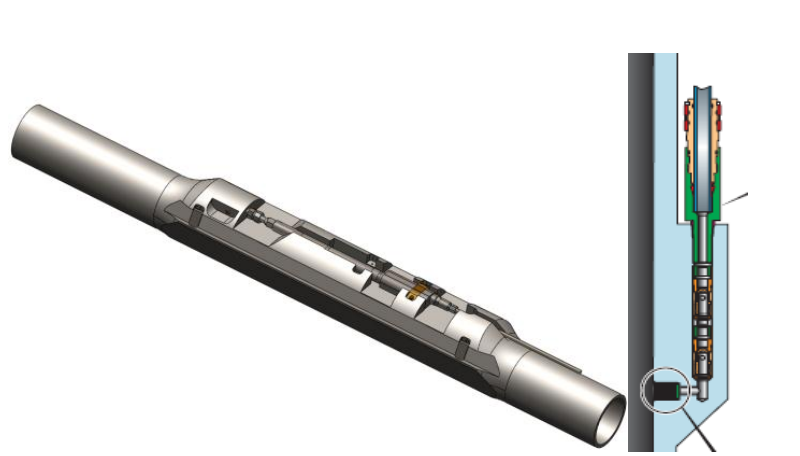
図 2. マンドレルとバルブを備えた非典型的なダウンホール化学薬品注入システムのスケッチ。このシステムは表面マニホールドに接続され、チューブの環状側にあるチューブ ハンガーを通して供給されて接続されます。化学物質注入マンドレルは伝統的に化学的保護を目的として井戸の奥深くに設置されています。
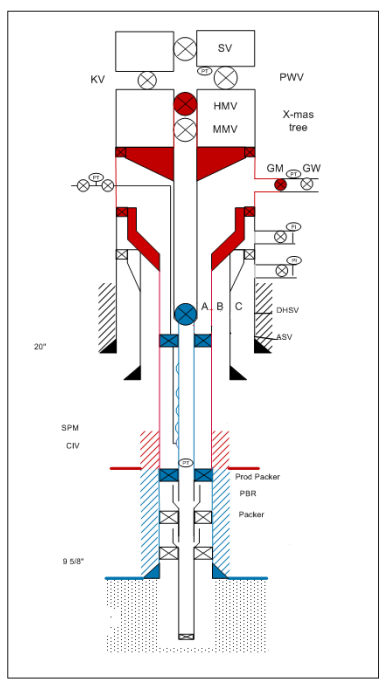
図 3. 典型的なウェルバリアの概略図,ここで、青色は一次ウェルバリアエンベロープを表します。この場合は製造チューブです。赤色は二次バリアエンベロープを表します。ケーシング。左側には化学薬品の注入が示されており、赤色でマークされた領域 (二次バリア) の製造チューブへの注入ポイントを示す黒い線が示されています。
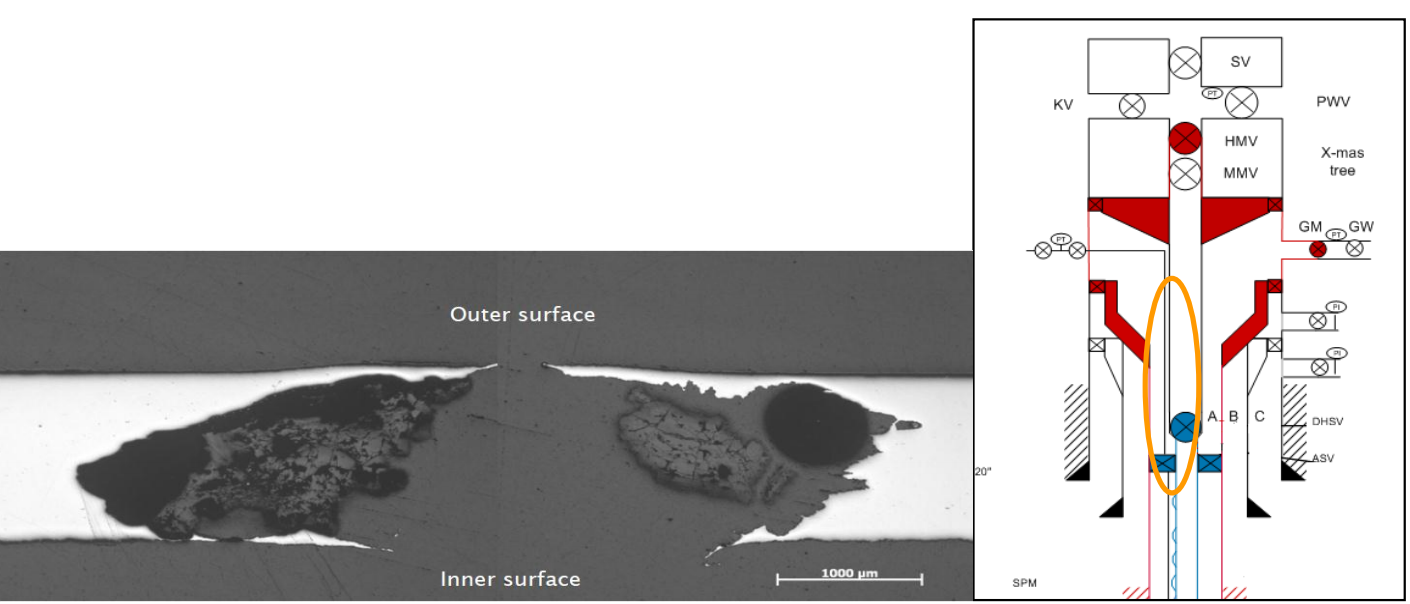
図 4. 3/8 インチ射出ラインの上部に見つかった穴。この領域は、典型的な井戸バリアの概略図のスケッチに示されており、オレンジ色の楕円でマークされています。
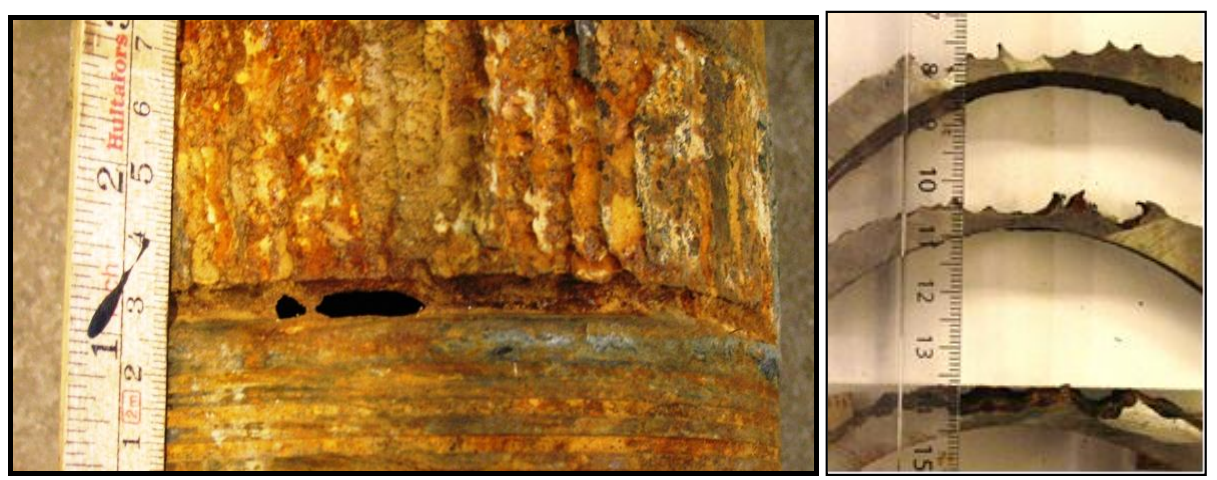
図 5. 7 インチ 3% クロム チューブへの深刻な腐食攻撃。この図は、穴のある化学薬品注入ラインから生産チューブにスケール防止剤を噴霧した後の腐食の様子を示しています。
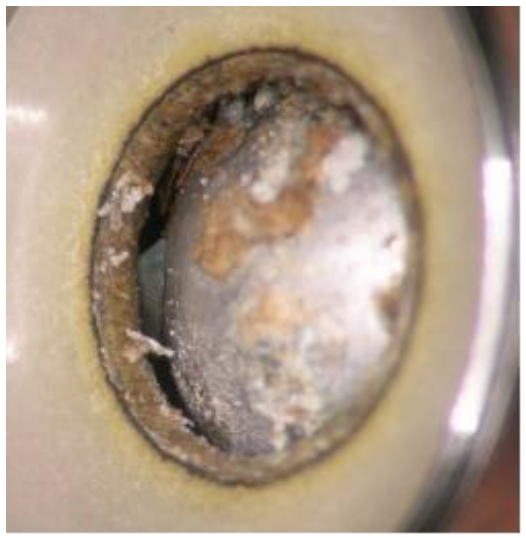
図 6. 薬液注入バルブ内で見つかった破片。この場合の破片は、いくつかの白っぽい破片に加えて、おそらく設置プロセスで発生した金属の削りくずでした。白い破片の検査により、注入された化学物質と同様の化学的性質を持つポリマーであることが判明しました。
投稿時間: 2022 年 4 月 27 日